Die casting is a manufacturing process used to produce metal parts with precise shapes and dimensions. It involves injecting molten metal into a steel mold, called a die, under high pressure. Once the metal cools and solidifies inside the die, the mold is opened, and the solidified part, known as the casting, is removed.
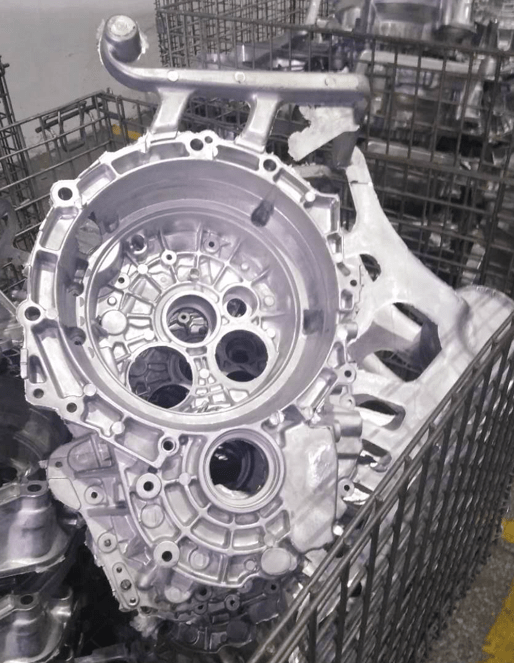
The die casting process is commonly used for mass production of parts made from non-ferrous metals, such as aluminum, zinc, copper, and magnesium. It offers several advantages, including:
1. Precision and complexity: Die casting allows the production of parts with intricate shapes and high dimensional accuracy, making it suitable for components that require tight tolerances.
2. High production rates: The process is capable of producing a large number of parts quickly and efficiently, making it cost-effective for mass production.
3. Smooth surface finish: Die-cast parts typically have a smooth surface, reducing the need for additional finishing processes.
The die casting process generally involves the following steps:
Mold preparation: The die (mold) is designed to create the desired shape of the part. It is typically made from steel and consists of two halves, the "cover die" and the "ejector die."
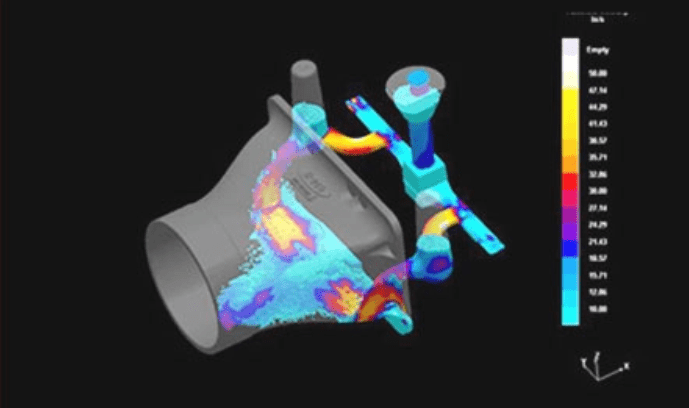
Melting the metal: The chosen metal is melted in a furnace to a specific temperature suitable for the die casting process.
Injection: The molten metal is forced into the die cavity at high pressure using a machine called a die casting machine.
Cooling and solidification: The molten metal cools and solidifies inside the die to take the shape of the cavity.
Ejection: Once the casting has solidified, the two halves of the die are opened, and the part is ejected from the mold.
Trimming and finishing: The casting may undergo additional processes such as trimming, removing any excess material, and surface finishing to meet the required specifications.
Die casting is used in various industries to manufacture components for automotive parts, consumer electronics, appliances, aerospace applications, and more. It is a widely employed technique for achieving high-quality, consistent, and cost-effective metal parts in large quantities.