The process of making ceramics involves several stages, including raw material preparation, forming, drying, firing, and glazing (optional). Ceramics are made from naturally occurring raw materials, such as clay, which is processed and shaped into the desired form before undergoing a firing process to achieve the final ceramic product. Here is an overview of the typical process to make ceramics:
Raw Material Preparation:
Clay Mining: The first step involves the extraction of clay from natural deposits through mining.
Clay Preparation: The mined clay is then purified, crushed, and mixed with other materials like feldspar, silica, and other additives to enhance its properties and workability.
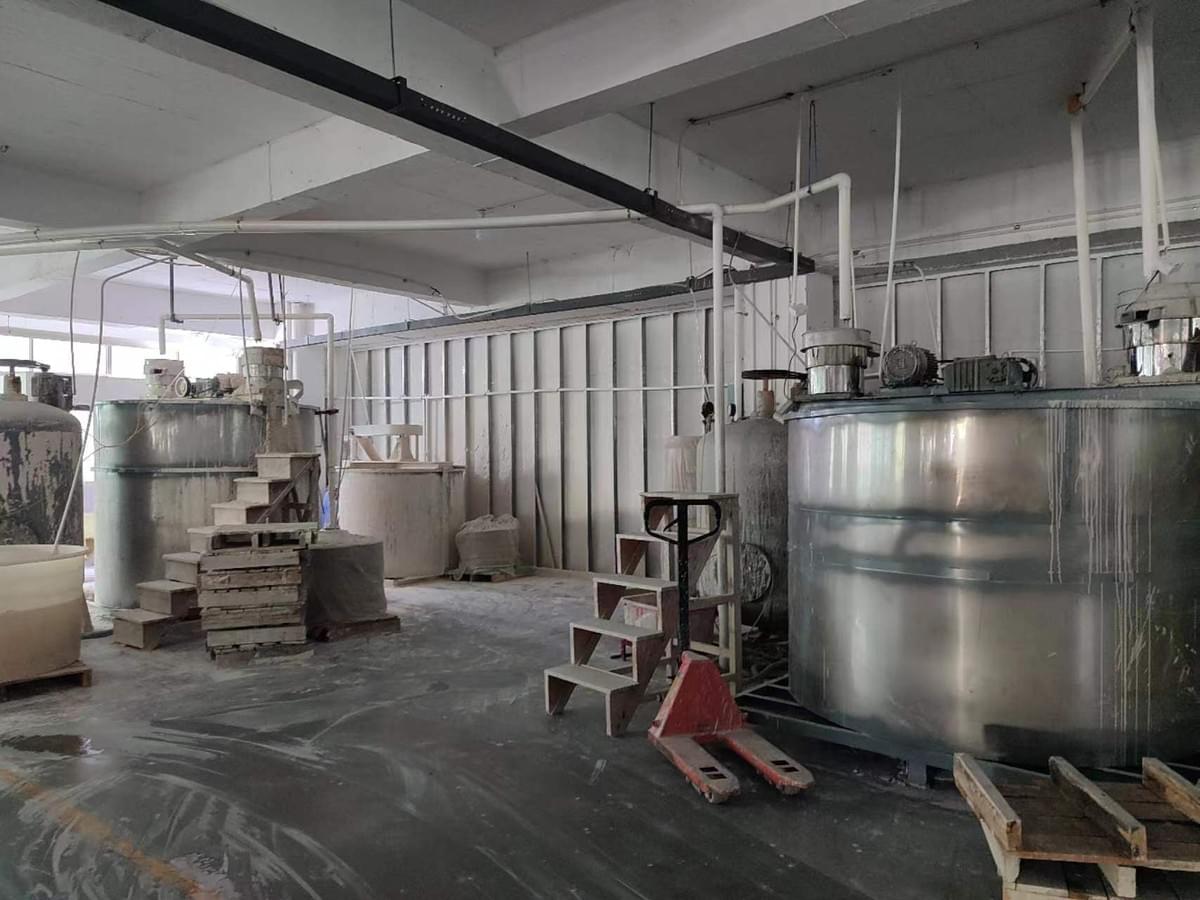
Forming:
Hand Forming: In traditional pottery, skilled artisans may shape the clay manually using techniques like hand-building or wheel-throwing.
Machine Forming: In modern ceramic production, machines like potters' wheels or molding presses are used for mass production to create consistent shapes.
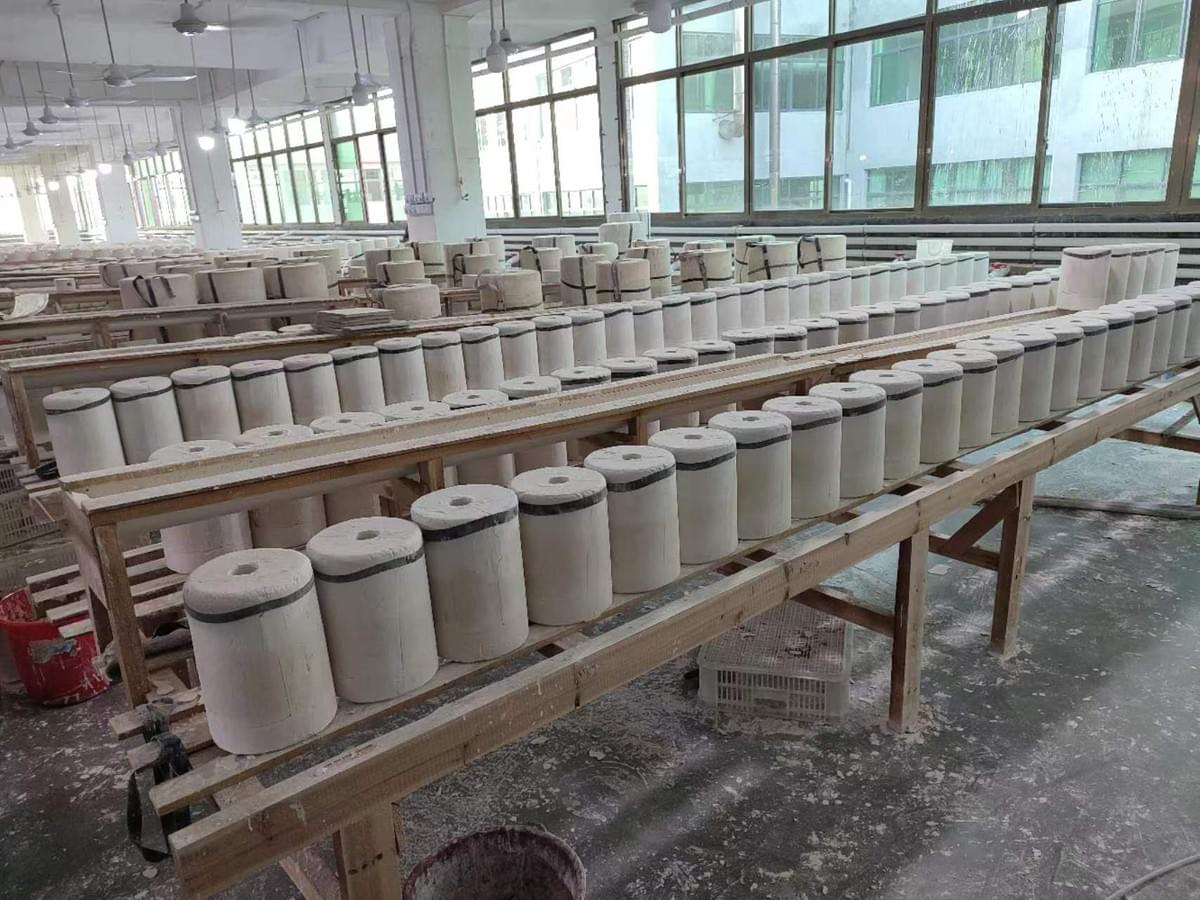
Drying:
After forming the clay into the desired shape, the ceramic pieces are left to air dry to reduce their moisture content. Proper drying is crucial to prevent cracking and warping during the firing process.
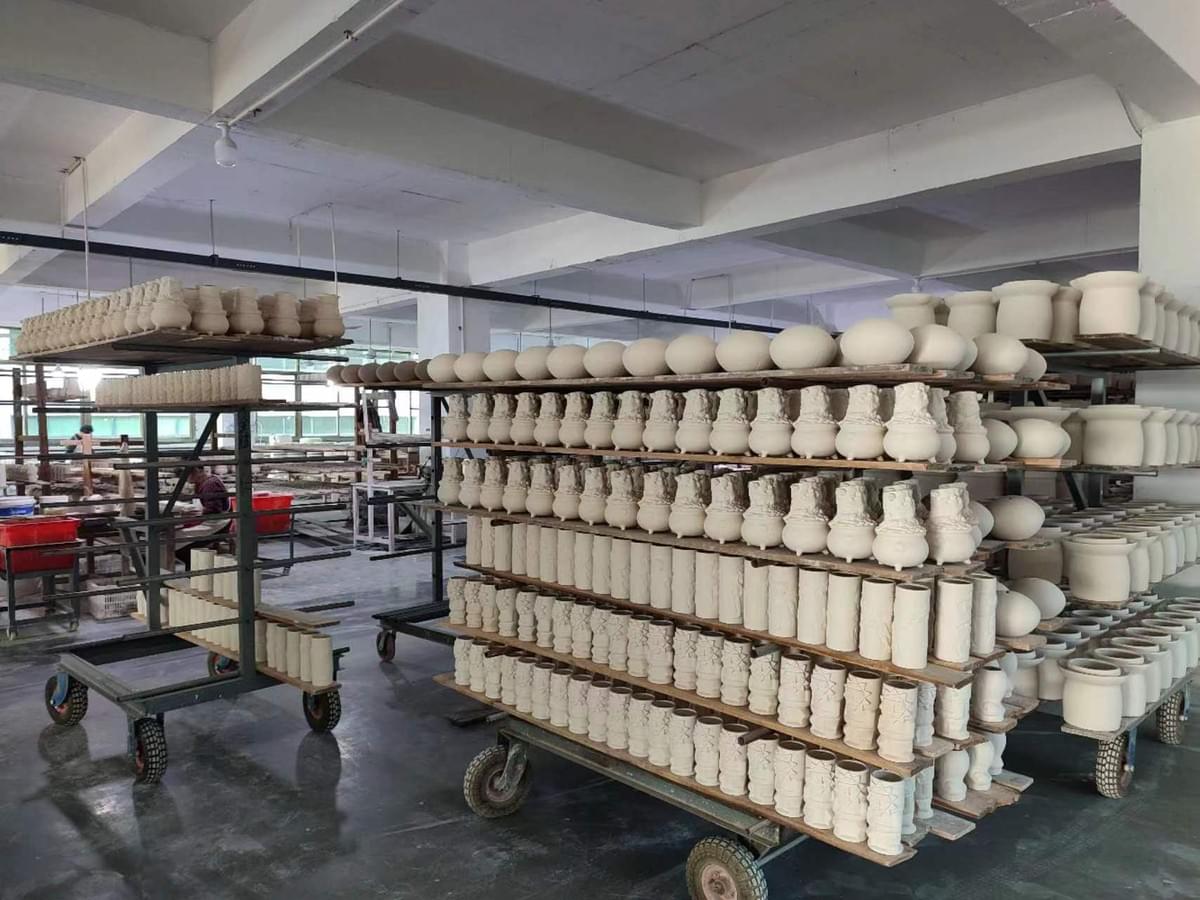
Firing:
Bisque Firing: The dried ceramic pieces are loaded into a kiln and subjected to the first firing, known as bisque firing. This firing is done at a relatively low temperature, typically between 800 to 1000 degrees Celsius, to remove any remaining moisture and make the pieces more durable for glazing.
Glaze Firing (Optional): If glazing is desired, the ceramic pieces are coated with a glaze – a glass-like substance – that provides a decorative or protective finish. The glazed pieces are then subjected to a second firing at a higher temperature, typically between 1100 to 1300 degrees Celsius, to melt the glaze and bond it to the ceramic surface.
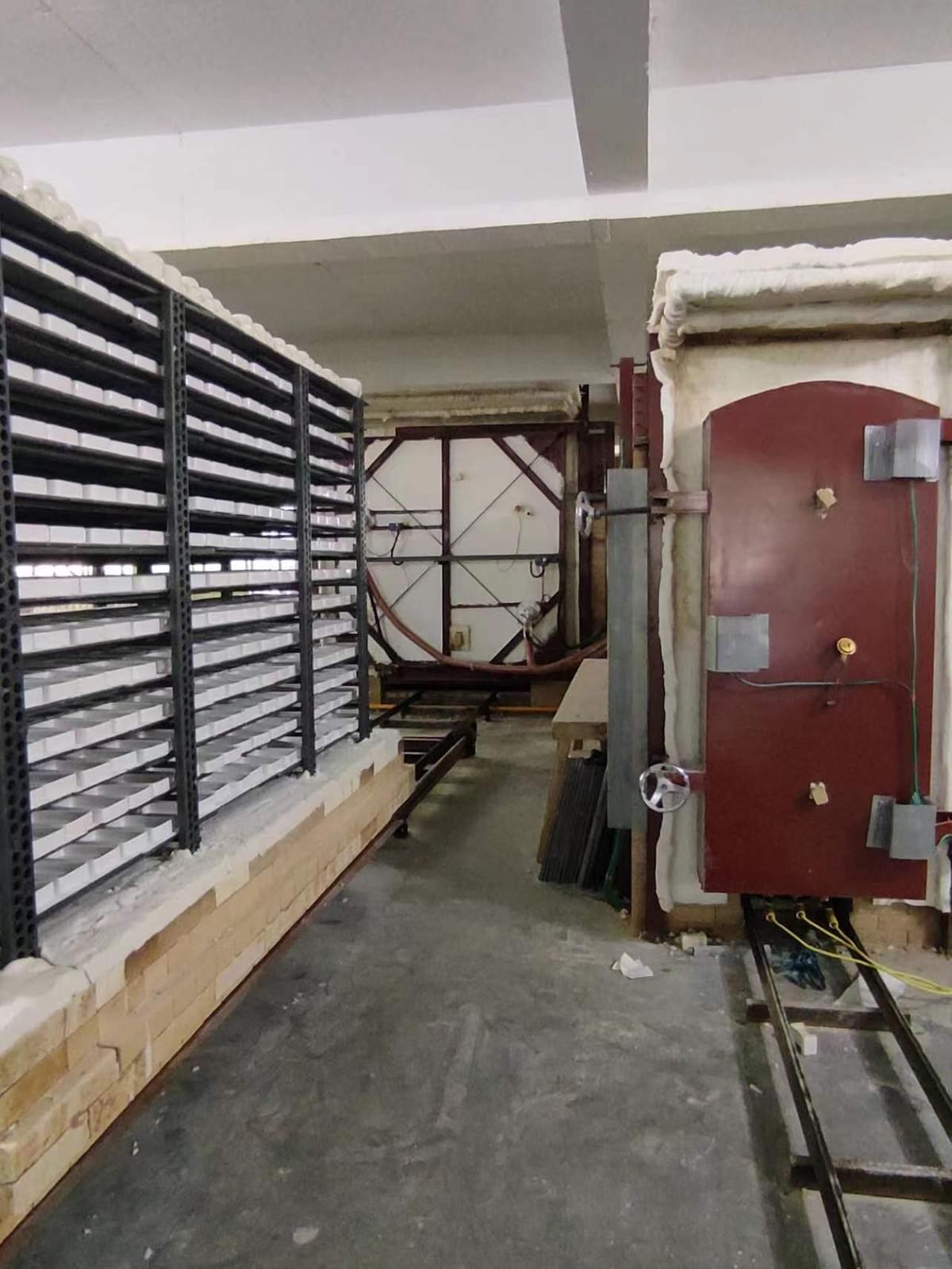
Cooling and Inspection:
After the firing process, the kiln is allowed to cool down slowly to prevent thermal shock and potential cracking of the ceramics. Once cooled, the ceramic pieces are inspected for quality and defects.
Finishing (Optional):
Depending on the desired final appearance and use, additional finishing processes like polishing, painting, or decorative techniques may be applied to the ceramics.
Quality Control:
Throughout the entire ceramic manufacturing process, quality control checks are performed to ensure that the final products meet the required specifications and standards.
It's important to note that the specific process and techniques used may vary depending on the type of ceramic being produced (e.g., pottery, porcelain, stoneware) and the level of automation in the manufacturing process. The firing temperature and duration also play a significant role in determining the ceramic's final characteristics, such as its strength, density, and appearance.